Cable and Wiring Harness – What it is, what it consists of
Wiring harnesses are an essential part of electronic systems and devices, allowing energy and electrical signals to be transported within a system and making it possible for the devices themselves to function.
In this text, we will explore the fundamental characteristics of wiring harnesses, the requirements they must fulfil and their role in the efficiency and reliability of systems.
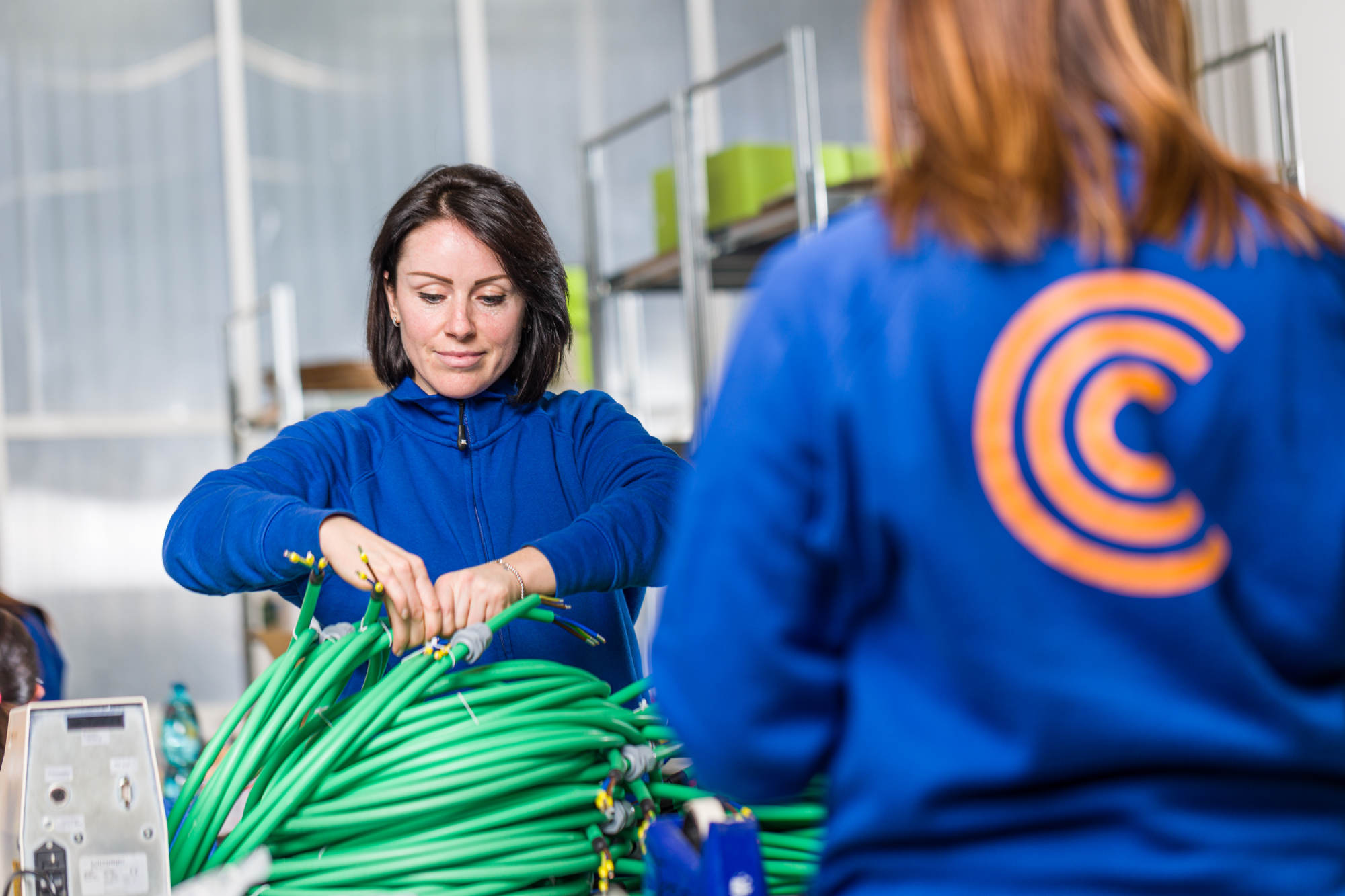
Cablotech technicians assemble custom electrical wiring harnesses
What a wiring harness is
A wiring harness is a set of cables, terminals and connectors used to convey power and electrical signals within a system. It is an essential part in many electronic devices, from computers to industrial equipment.
They are designed to meet the diverse and specific needs of the system they are used in, such as those found in industrial equipment that must be able to withstand extreme temperatures, vibrations and extreme temperature environments.
The design and implementation of wiring requires specialised skills and the use of specific equipment. Our company is able to offer codesign and implementation services for the wiring harnesses for the efficient and reliable operation of systems.
The quality of these services directly influences the operation of an entire structure. In fact, correctly designed and implemented wiring ensures a stable and reliable flow of energy and information.
What a wiring harness consists of
We have seen how a wiring harness plays an extremely important role in today’s infrastructures, constituting an essential part in the correct functioning of the machines, apparatuses and devices we use on a daily basis.
Wiring harnesses are also characterised by their considerable structural complexity, which varies greatly according to the various parameters and fields of use.
Wiring harnesses consist of various elements, including cables, terminals, connectors, plugs, sockets and splices, etc.
Cables are conductors made of copper, or other metals, carrying electrical current in some cases and exchanging data and information in others; there are different types, each of which has specific characteristics that make them suitable for certain applications. For example, fibre optic cables are used to carry high-speed and high-precision signals, while coaxial cables are used to carry television and radio signals.
Terminals are an essential part of the wiring as incorrect seaming can compromise its correct functioning. The terminals are seamed with the aid of specific applicators and respecting the height parameters, a value that is checked with annually calibrated special instruments.
Another fundamental element of seaming is the press that is used together with the applicator to perform crimping, and is subject to periodic calibration.
Instead, connectors are used to connect cables to each other and to interface with the various electrical parts within equipment. There are different types of connectors and each is designed to work with a specific type of cable and to connect to specific equipment.
Wiring also includes other components, such as heat-resistant sheaths and cable sheaths that serve to protect cables in difficult environments and extreme climatic conditions.
In general, the design of a wiring harness requires a careful assessment of the needs of the system in which it will be used and the selection of components suitable for the expected operating conditions, to ensure its reliability and correspondence to required specifications.
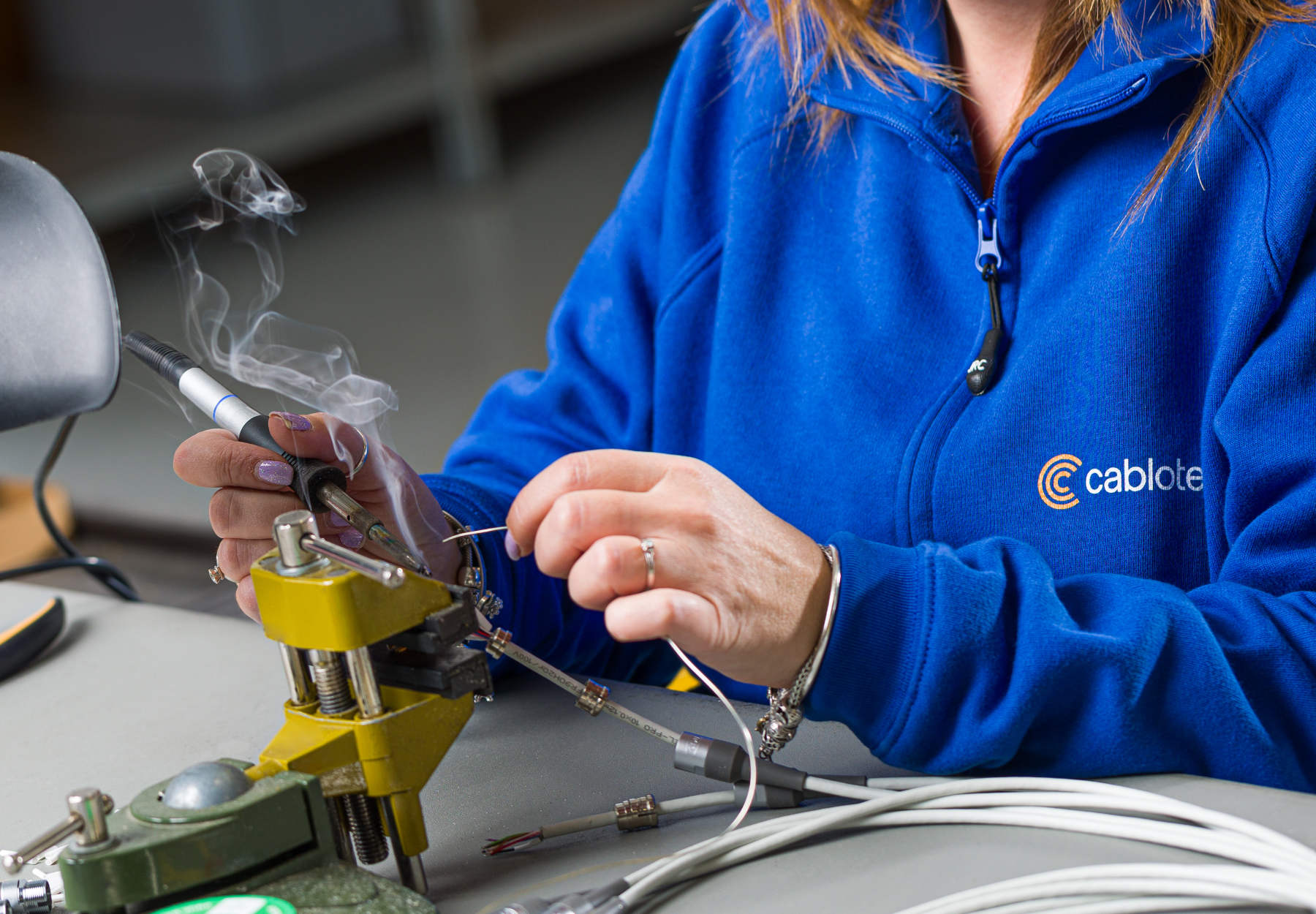
Steps for the creation of a wiring harness
Cutting and Stripping: this is the first stage in the creation of cabling.
The cables must be cut to the appropriate length to suit the system in which they will be used.
They are cut automatically using PC-controlled electronic cutters and strippers. In this first phase, the electrical cable must be carefully checked to avoid damage to it before production.
The cable cross-section plays an important role, as it is able to guarantee the correct and stable transmission of energy and electrical signals within the system.
In addition, the voltage, current, frequency and temperature conditions that the cables will be subjected to must also be taken into account.
Stripping is the unsheathing and cleaning of the cable, if a shield is present; it is the phase in which the conductors are prepared for the subsequent seaming.
In the case of unipolar conductors, the cutting and stripping activities can be grouped in a single phase whereas in the case of compound cables with several conductors, there is a first phase of cutting and unsheathing and a second phase in which the individual conductors are worked on for stripping.
This is an important step, because correct execution ensures a reliable and secure connection between wires and equipment.
This can be carried out manually or using automatic tools.
Seaming: it is the crimping of terminals to conductors using special tools working on semi-automatic or automatic presses
Cable bundling: it is a technique used to organise and protect cables within a cabling system.
It consists of grouping the cables together using special clamps or cable ties that can be made of metal or plastic, depending on requirements, to guarantee their correct position and protection from mechanical stress.
It is important to use appropriately sized clamps or cable ties to avoid damaging the cables during fixing and to ensure a secure seal that can withstand the environmental and mechanical conditions they are exposed to.
In addition, it is also very important to consider the position of bundling, which must be chosen to avoid pressure on one point of the cables, which can cause damage, and must be easily accessible for any maintenance work.
Marking: Cable marking is a common practice in the construction of a wire harness to allow each individual cable to be uniquely identified. It consists of identifying each cable or wire within the system and the ways in which it can be done vary depending on the type of cable and the customers’ needs and requirements.
For unipolar cables, this is a marking that can be either ink-jet or hot-foil stamped and takes place directly at the cutting and stripping stage.
Instead, for compound cables it is performed by applying adhesive labels and tags to the cable.
Marking has multiple purposes, one of which is to make system maintenance easier: if a cable needs to be replaced, it is much easier to identify it, making the whole process quicker and easier.
Mechanical protection: Wiring can be protected by heat-resistant sheathing, braided sheathing, pvc sheathing, or glass elastomer tubing, cable ducts, etc to ensure that it is protected from mechanical damage, moisture, dust and corrosion.
In many cases, it is necessary to weld the wires.
The welding process consists of joining parts using tin heated to the appropriate temperature.
Looking for more information about our services?
Discover what we can do for your company.
Next Event: MECSPE
We are excited to participate in MECSPE 2025, the leading trade fair for the subcontracting industry.
Visit us at Hall 28 – Stand B01 from March 5th to 7th, 2025!
Discover how Cablotech is driving innovation in electrical wiring, panels and electromechanical assembly.