Wiring Harness - How it is made by Cablotech
Educational
Wiring harnesses are an essential part of electronic systems and devices, allowing energy and electrical signals to be transported within a system and making it possible for the devices themselves to function.
In this article we will see how it is manufactured by Cablotech and how the design and installation of a suitable system is essential to ensure the correct functioning of the wiring of electronic systems and electrical panels.
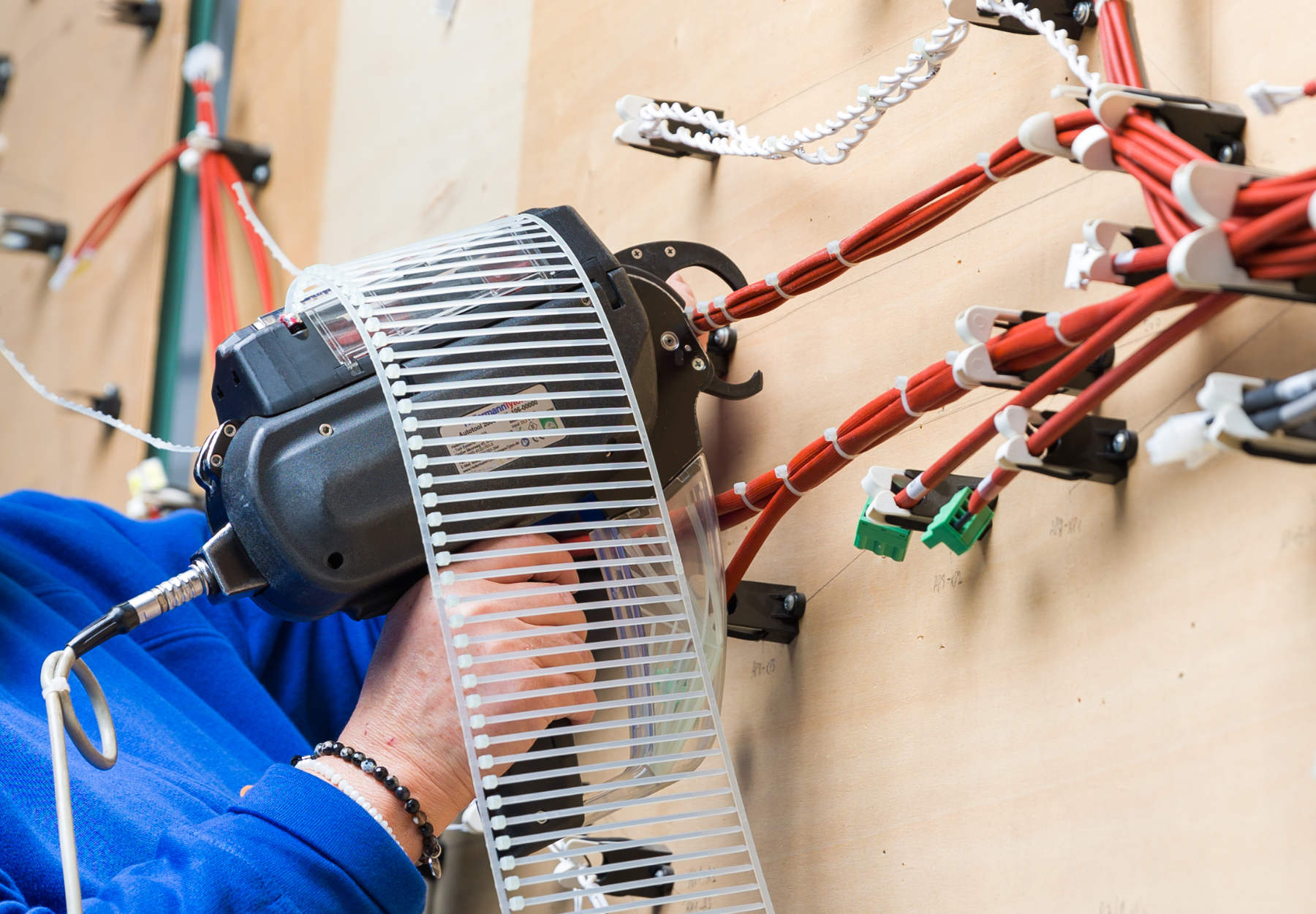
Cablotech technicians assemble preformed wiring harnesses with automatic wrapping machine
How Cablotech manufactures wiring harness
In the previous article we looked at what a wiring harness is and what it consists of, now we will find out how it is manufactured by Cablotech.
At Cablotech we have specialised for over 25 years in the creation of electrical cabling using state-of-the-art equipment, guaranteeing high standards of quality, complete customisation and an ad hoc service for every type of industry.
We use automatic machines to perform various operations such as the cutting, stripping, marking and seaming of cables.
The first step is to program the automatic machines to perform the required operations, which can be achieved using special software to set the cutting, stripping and seaming data.
Once the machines have been programmed, the cables are prepared and loaded into the automatic machine.
The cabling production process may start from a customer’s technical drawing, or from an idea of the customer, or even from a sample provided by the customer;
the technical department screens every step.
We then interface with our suppliers to evaluate the components to ensure that they meet the required characteristics as closely as possible.
All these operations are performed automatically, ensuring that the cables are correctly prepared for the next step.
After the cutting and stripping phase, the cable is ready to be seamed with its terminals, verifying it has been correctly executed.
The cable can then be sheathed and connected to specific connectors.
Finally, an electrical and visual cross-check is carried out, i.e. the person who performs the test is not the person who performed the cabling.
At the end of the process, the wiring harness is packed and shipped or it can be taken to assembly to be wired into an electrical cabinet or into other electromechanical equipment.
Quality controls on Cablotech wiring harness
Quality control is a fundamental element in the creation of cabling; the standards on which our controls are based allow us to
limit errors as far as possible, ensuring the cabling meets our customers’ specific requirements.
Finally, we are able to qualitatively identify each individual harness we send to the customer via QR code.
Looking for more information about our services?
Discover what we can do for your company.
Next Event: MECSPE
We are excited to participate in MECSPE 2025, the leading trade fair for the subcontracting industry.
Visit us at Hall 28 – Stand B01 from March 5th to 7th, 2025!
Discover how Cablotech is driving innovation in electrical wiring, panels and electromechanical assembly.
Cable and Wiring Harness - What it is, what it consists of
Educational
Wiring harnesses are an essential part of electronic systems and devices, allowing energy and electrical signals to be transported within a system and making it possible for the devices themselves to function.
In this text, we will explore the fundamental characteristics of wiring harnesses, the requirements they must fulfil and their role in the efficiency and reliability of systems.
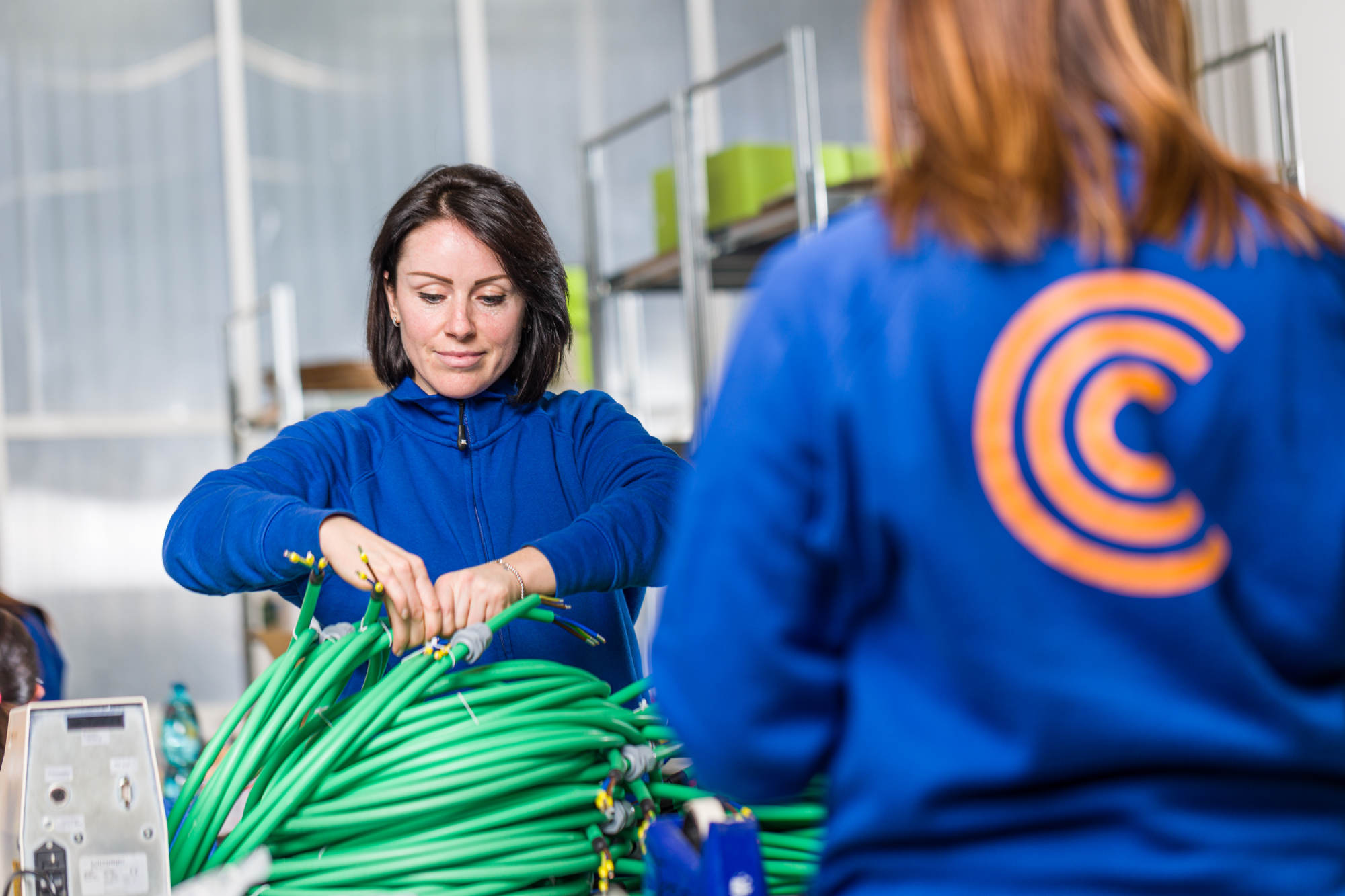
Cablotech technicians assemble custom electrical wiring harnesses
What a wiring harness is
A wiring harness is a set of cables, terminals and connectors used to convey power and electrical signals within a system. It is an essential part in many electronic devices, from computers to industrial equipment.
They are designed to meet the diverse and specific needs of the system they are used in, such as those found in industrial equipment that must be able to withstand extreme temperatures, vibrations and extreme temperature environments.
The design and implementation of wiring requires specialised skills and the use of specific equipment. Our company is able to offer codesign and implementation services for the wiring harnesses for the efficient and reliable operation of systems.
The quality of these services directly influences the operation of an entire structure. In fact, correctly designed and implemented wiring ensures a stable and reliable flow of energy and information.
What a wiring harness consists of
We have seen how a wiring harness plays an extremely important role in today’s infrastructures, constituting an essential part in the correct functioning of the machines, apparatuses and devices we use on a daily basis.
Wiring harnesses are also characterised by their considerable structural complexity, which varies greatly according to the various parameters and fields of use.
Wiring harnesses consist of various elements, including cables, terminals, connectors, plugs, sockets and splices, etc.
Cables are conductors made of copper, or other metals, carrying electrical current in some cases and exchanging data and information in others; there are different types, each of which has specific characteristics that make them suitable for certain applications. For example, fibre optic cables are used to carry high-speed and high-precision signals, while coaxial cables are used to carry television and radio signals.
Terminals are an essential part of the wiring as incorrect seaming can compromise its correct functioning. The terminals are seamed with the aid of specific applicators and respecting the height parameters, a value that is checked with annually calibrated special instruments.
Another fundamental element of seaming is the press that is used together with the applicator to perform crimping, and is subject to periodic calibration.
Instead, connectors are used to connect cables to each other and to interface with the various electrical parts within equipment. There are different types of connectors and each is designed to work with a specific type of cable and to connect to specific equipment.
Wiring also includes other components, such as heat-resistant sheaths and cable sheaths that serve to protect cables in difficult environments and extreme climatic conditions.
In general, the design of a wiring harness requires a careful assessment of the needs of the system in which it will be used and the selection of components suitable for the expected operating conditions, to ensure its reliability and correspondence to required specifications.
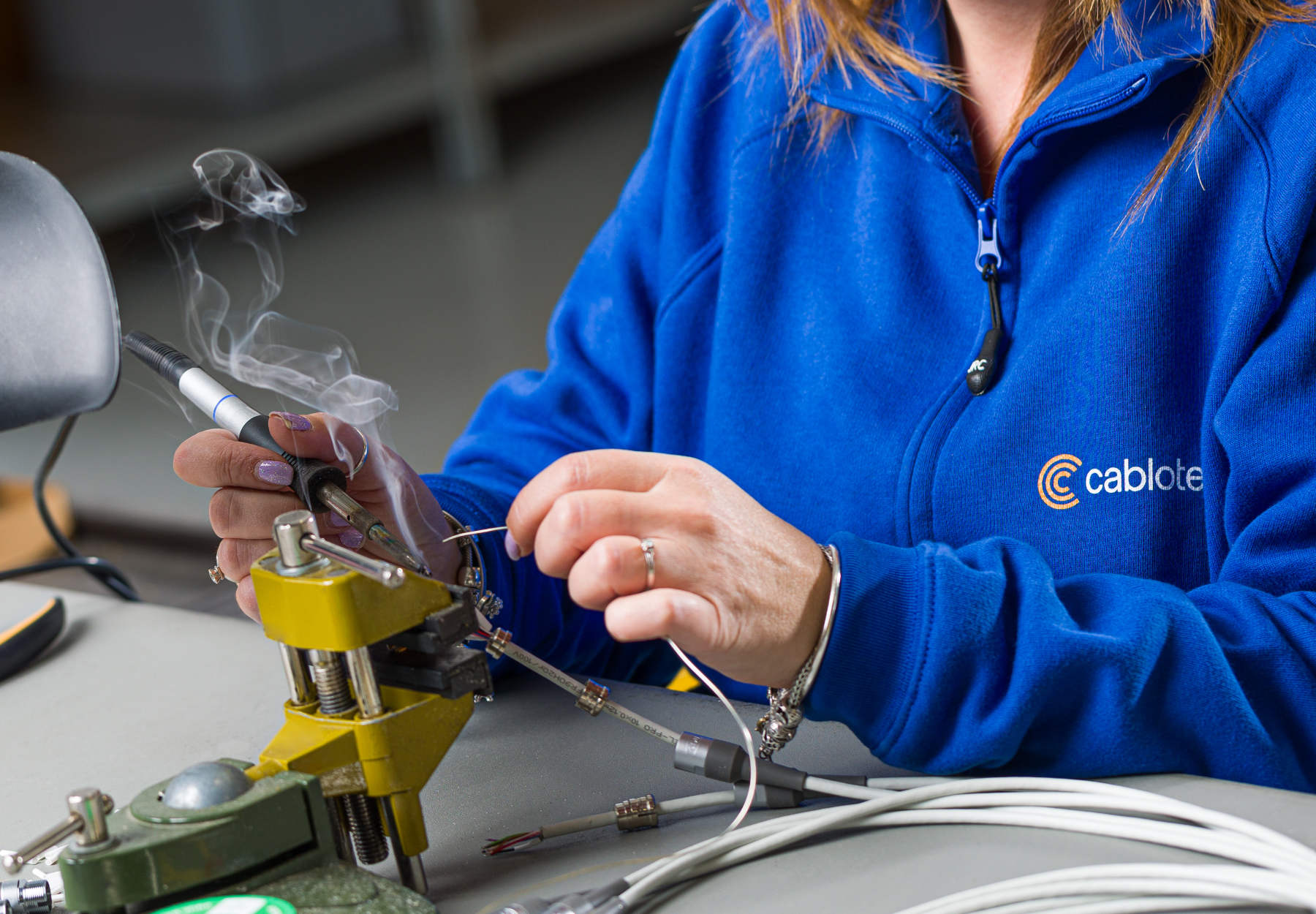
Steps for the creation of a wiring harness
Cutting and Stripping: this is the first stage in the creation of cabling.
The cables must be cut to the appropriate length to suit the system in which they will be used.
They are cut automatically using PC-controlled electronic cutters and strippers. In this first phase, the electrical cable must be carefully checked to avoid damage to it before production.
The cable cross-section plays an important role, as it is able to guarantee the correct and stable transmission of energy and electrical signals within the system.
In addition, the voltage, current, frequency and temperature conditions that the cables will be subjected to must also be taken into account.
Stripping is the unsheathing and cleaning of the cable, if a shield is present; it is the phase in which the conductors are prepared for the subsequent seaming.
In the case of unipolar conductors, the cutting and stripping activities can be grouped in a single phase whereas in the case of compound cables with several conductors, there is a first phase of cutting and unsheathing and a second phase in which the individual conductors are worked on for stripping.
This is an important step, because correct execution ensures a reliable and secure connection between wires and equipment.
This can be carried out manually or using automatic tools.
Seaming: it is the crimping of terminals to conductors using special tools working on semi-automatic or automatic presses
Cable bundling: it is a technique used to organise and protect cables within a cabling system.
It consists of grouping the cables together using special clamps or cable ties that can be made of metal or plastic, depending on requirements, to guarantee their correct position and protection from mechanical stress.
It is important to use appropriately sized clamps or cable ties to avoid damaging the cables during fixing and to ensure a secure seal that can withstand the environmental and mechanical conditions they are exposed to.
In addition, it is also very important to consider the position of bundling, which must be chosen to avoid pressure on one point of the cables, which can cause damage, and must be easily accessible for any maintenance work.
Marking: Cable marking is a common practice in the construction of a wire harness to allow each individual cable to be uniquely identified. It consists of identifying each cable or wire within the system and the ways in which it can be done vary depending on the type of cable and the customers’ needs and requirements.
For unipolar cables, this is a marking that can be either ink-jet or hot-foil stamped and takes place directly at the cutting and stripping stage.
Instead, for compound cables it is performed by applying adhesive labels and tags to the cable.
Marking has multiple purposes, one of which is to make system maintenance easier: if a cable needs to be replaced, it is much easier to identify it, making the whole process quicker and easier.
Mechanical protection: Wiring can be protected by heat-resistant sheathing, braided sheathing, pvc sheathing, or glass elastomer tubing, cable ducts, etc to ensure that it is protected from mechanical damage, moisture, dust and corrosion.
In many cases, it is necessary to weld the wires.
The welding process consists of joining parts using tin heated to the appropriate temperature.
Looking for more information about our services?
Discover what we can do for your company.
Next Event: MECSPE
We are excited to participate in MECSPE 2025, the leading trade fair for the subcontracting industry.
Visit us at Hall 28 – Stand B01 from March 5th to 7th, 2025!
Discover how Cablotech is driving innovation in electrical wiring, panels and electromechanical assembly.
The electrical panel: how it is made at Cablotech
Educational
The electrical panel is an energy-sorting centre, essential because it powers all sockets, lights and electronic devices. It is built in compliance with the highest safety standards to protect consumers and people.
This article will address in detail how the Cablotech technicians create one.
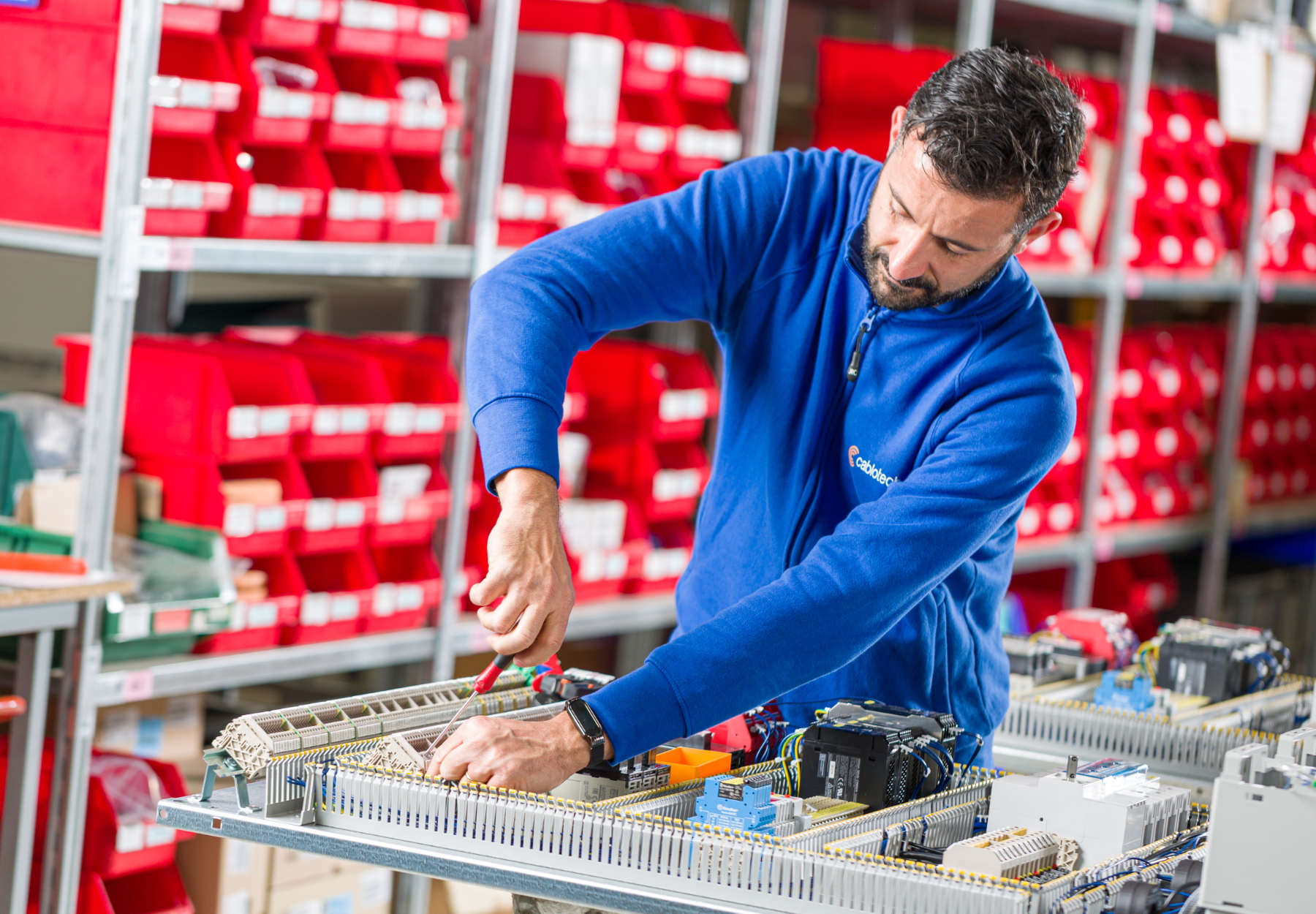
Switchboards manufacturing by Cablotech technicians
How Cablotech manufactures Electrical Panels
In the previous article we found out what an electrical panel is and what functions it performs, now we will cover in detail how it is made by Cablotech.
Cablotech activity focuses on Machine On Board electrical panels and
electrical panels for Diagnostics.
There are numerous essential steps to create an industrial electrical panel. Here at Cablotech we support the customer in co-designing to identify all the preparation diagrams and procedures to create the electrical panel.
The customer provides us with the wiring diagram and layout of the electrical panel.
Once we have completed the component layout and chosen the wiring diagram with the relevant conductor cross-sections and colours, we move on to the next phase: determining the cable lengths after which they are cut and trimmed.
With the aid of CAD or even by physically inspecting them in the electrical box, the aim is to prepare an electronic sheet that can be read by the cutting machines, which will be able to cut and, above all, mark each conductor, according to the indications provided.
Once it has been ensured the cable cutting process has been optimally performed, the following step is seaming on presses or using hand pliers for special crimping.
Depending on the case and requirements, the cables may be subject to further modifications, such as additional marking by means of tags or sheathing. There are various types of sheaths: mesh, PVC, flexible, etc. and they are essential to protect cables from passages that could be potentially damaging to the cable insulation thereby always ensuring compliance with the safety regulations.
If necessary, connectors are also applied: therefore, once the seaming of the appropriate terminals has been completed, they are inserted into the connector, always keeping the previously designed wiring diagram as the main reference point.
In the electrical box, the components and terminals are labelled to catalogue the functions of each one; after this operation, cable ducts and cable glands are arranged for the passage of cables to then be able to proceed with their wiring once the seaming is complete.
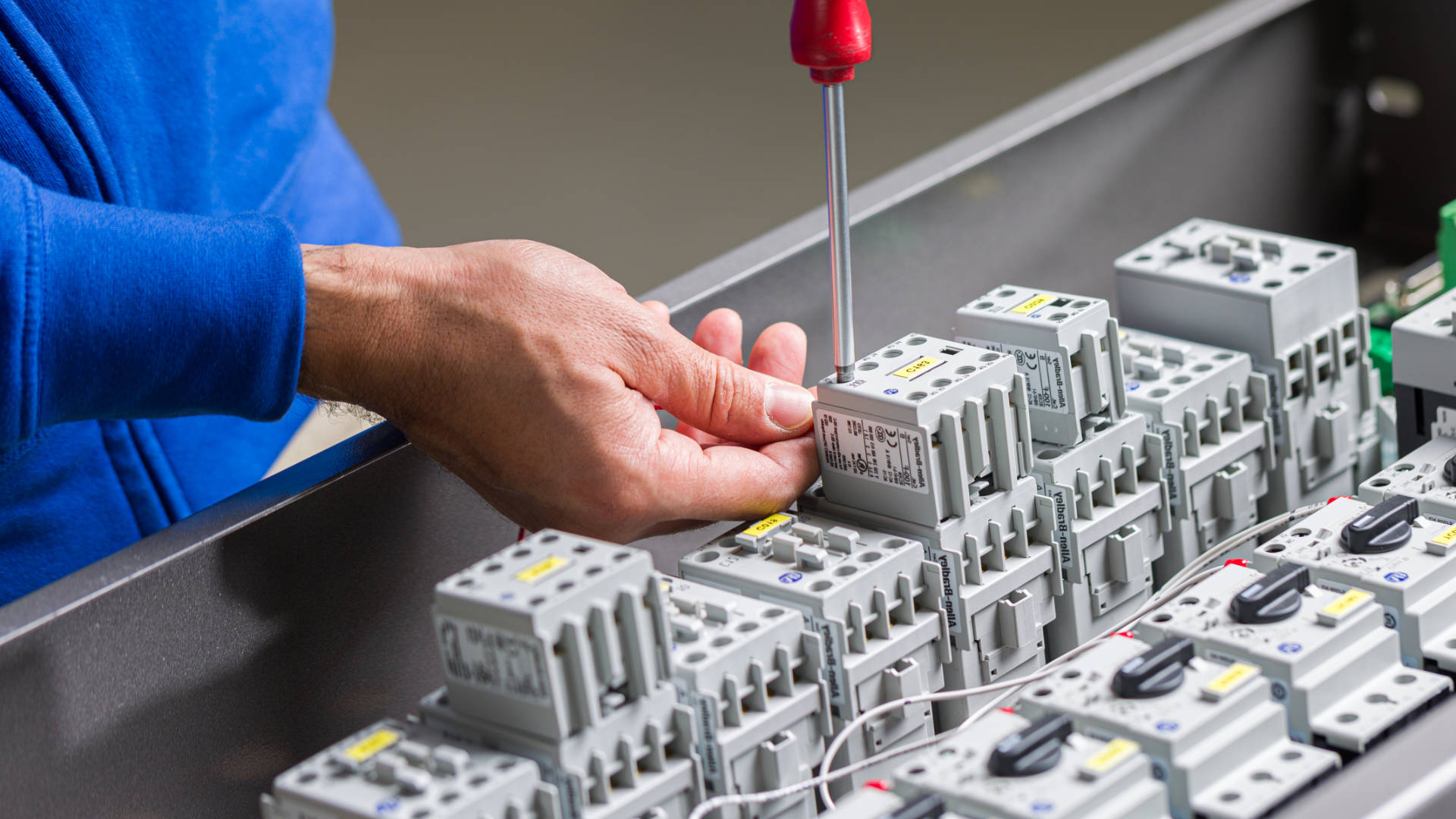
The next step is to lay the cables in the electrical box with the aid of specially calibrated screwdrivers, or even with screwdrivers in the case of delicate or particularly complicated tightening. All this is always carried out with reference to the wiring diagram or to the previous electronic wire, which also contains information on the individual conductors and their insulation.
The technicians will also use torque spanners to check tightening torques, further fine-tuning the system.
Once all these operations, of varying duration and complexity, have been completed, the following step is a visual or even cross-check, using an operator who has not contributed to the construction of the electrical panel.
For additional safety for the benefit of the electrical panel and the customer, an electrical test is also carried out, performed by technicians with regular PES/PAV certification.
At this point, the electrical panel is ready to be packed, labelled and shipped to the customer’s selected location.
Thanks to our long-standing and proven experience in electrical wiring, switchboards and electromechanical assemblies, for over 25 years our flagship has been the customisation of our services according to customer requirements.
We focus on meeting users’ needs, contributing to the realisation of small and large customised projects.
We pay attention to every step of the process and perform acceptance tests and final overhauls before delivering the products.
Looking for more information about our services?
Discover what we can do for your company.
Next Event: MECSPE
We are excited to participate in MECSPE 2025, the leading trade fair for the subcontracting industry.
Visit us at Hall 28 – Stand B01 from March 5th to 7th, 2025!
Discover how Cablotech is driving innovation in electrical wiring, panels and electromechanical assembly.
The electrical panel: what it is and its functions
Educational
The electrical panel is an energy-sorting centre, essential because it powers all sockets, lights and electronic devices. It is built in compliance with the highest safety standards to protect consumers and people.
This article will address in detail what an electrical panel is and what types it can be classified into.
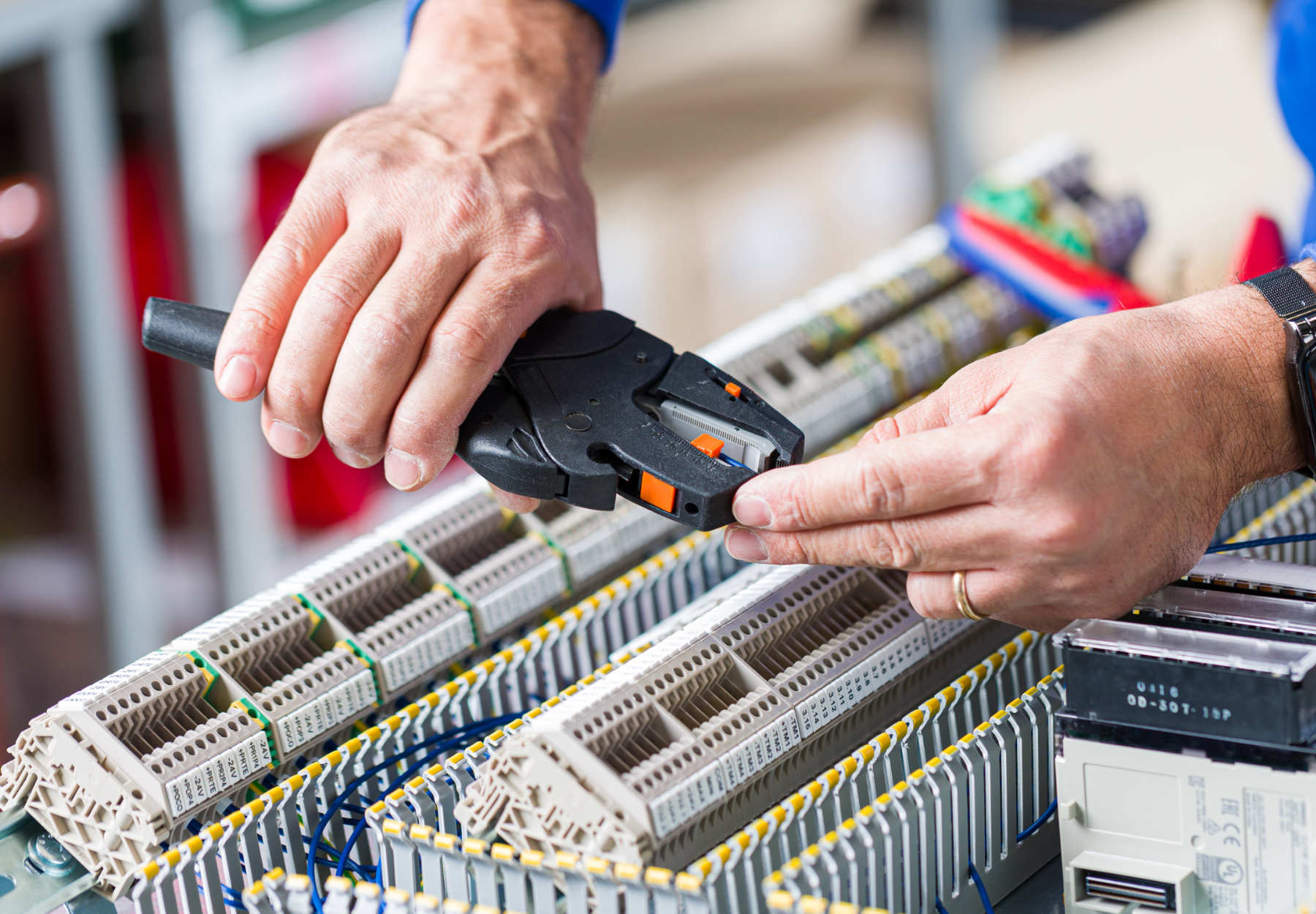
Switchboards manufacturing by Cablotech technicians
What an Electrical Panel is
A fundamental premise is to distinguish between a civil and an industrial electrical panel, as the elements that compose the electrical panel itself change.
In the civil sector, the electrical panel constitutes the fundamental part of the electrical system and has the function of powering the entire circuit, protecting it at the same time from possible overheating and preventing users from accidental electrocution.
It is a metal or plastic structure designed to distribute electricity and to control a wide variety of electronic devices in a building.
The perfect implementation of an electrical installation in compliance with Directive 2014/35/EU and Legislative Decree 86/2016 concerning the safety guarantees the electrical equipment must possess is very important; it establishes that all liability, in the event of an accident, is attributable to the manufacturer of the equipment.
It is important that professionals perform maintenance on the electrical panel as failure to do so could represent a safety risk. If you do not have the skills to service the electrical panel yourself, ask a professional for help.
In the industrial field, in addition to the above regulations, there are also IEC regulations governing the design and construction of an industrial system. These are particularly strict, as this is a complex task for which strict safety protocols must be followed. For cables, European regulations require the use of CE-marked cables, while American regulations require UL-marked ones.
Depending on the country of reference, in fact, the characteristics governing the use of legitimate cables change, as the intended use changes.
Types of Electrical Panels
Electrical panels can have different sizes and materials, depending
on their use and requirements in terms of space, degree of protection from atmospheric agents and the number of devices to be kept active and controlled.
The flush-mounted electrical panel is mainly used for industrial electrical panels.
The wall-mounted electrical panel is protruding, leaning against the wall, and consequently takes up more space in the room where it is fitted.
Indoor and outdoor electrical panels are distinguished by their degree of protection: the outdoor ones are defined as “watertight”, as they are insulated from water, liquids in general and humidity, as well as from atmospheric agents.
Then there is a further difference in terms of the voltage handled by the panel:
- Low-voltage electrical panels, i.e., less than 1Kv
- Medium voltage electrical panels, between 1 and 30Kv
- High-voltage electrical panels, between 30 and 150Kv
- Very high voltage electrical panels, which handle energy above 150Kv
Obviously, this difference in voltage will also influence the amount of electrical charge that the system will handle and thus its structural characteristics, as well as its actual location.
This and other factors determine those small and large differences between a civil and an industrial system, consequently also changing the elements that compose the electrical panel itself.
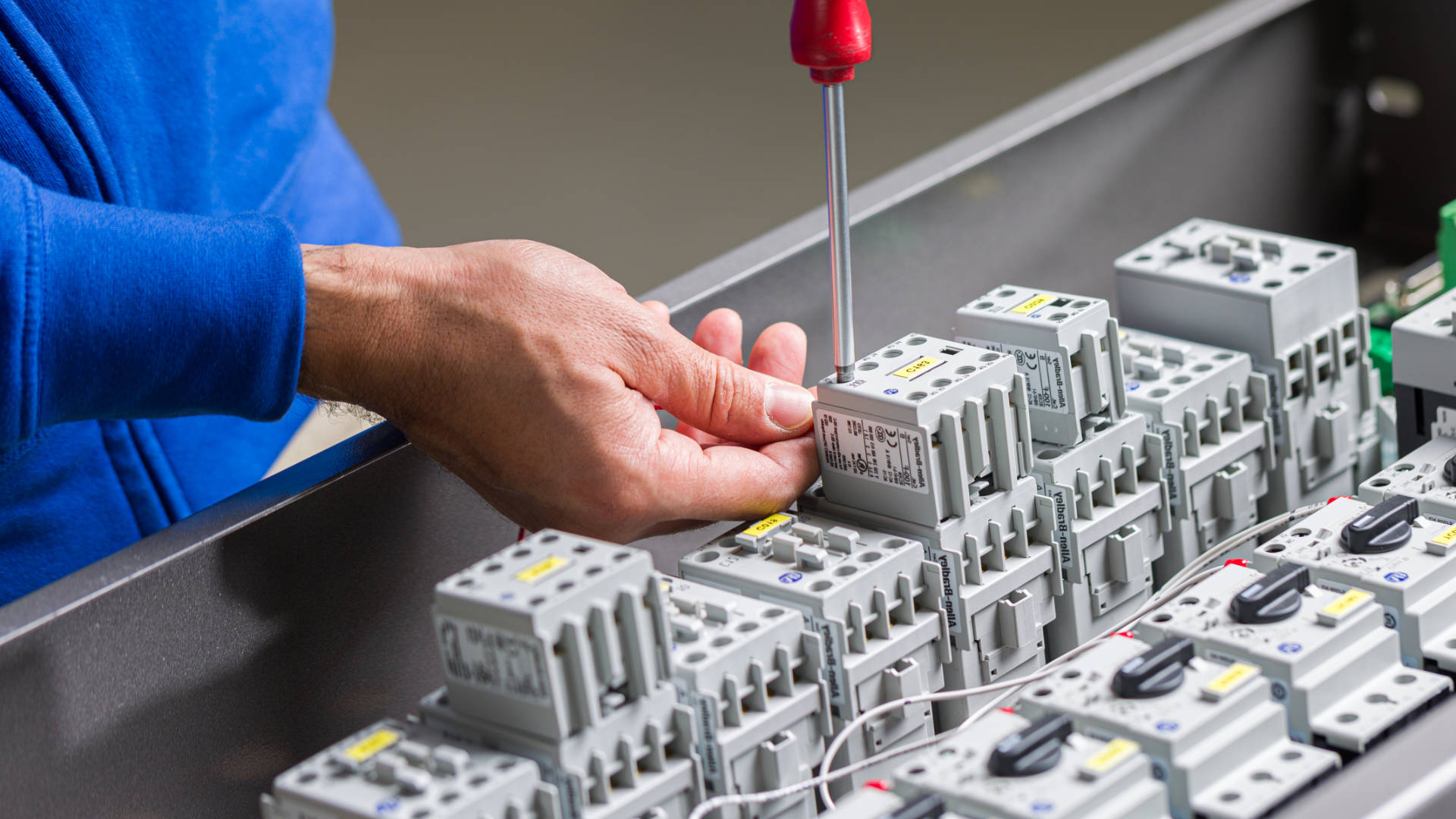
Functions performed by the electrical panel
Further differences persist in terms of the functions performed by the Electrical Panel.
- Distribution electrical panels are responsible for distributing power, supplying power and protecting users. They have the function of bringing power to junction boxes and to all the various electrical devices. They usually have 400V three-phase voltage with neutral, 230V three-phase or single-phase voltage with neutral and protection ratings from IP30 to IP65.
Its components are always accessible as it is necessary to ensure both the correct functioning of the devices connected to it and the safety of the operators using the system. It is the type of panel used in the civil sector. - Automation electrical panels are responsible for the command and control of automated equipment and electrical machines. They contain so-called “motor protector” switches, AC3 category meters, inverters, soft starts, PLCs, relays and electrical wiring. They are applicable in a wide range of areas as they can automate any type of function performed by machines: from simple start-up to managing much more sophisticated control and regulation processes.
Considering their complexity and function, they are particularly suitable for industrial use: industrial machines and production facilities will benefit greatly from command, control, and protection equipment managed by electrical panels, saving considerable time and manual energy.
Their placement also leaves some freedom of choice as they can be installed either on the machine itself or nearby, making the installation itself easier and more arbitrary. In any case, they are assembled in such a way that they are not accessible, leaving only push-buttons and indicator lights available. Therefore, once the initial configuration is set up it is important that the settings are in no way changed. The industrial electrical panel, once configured, should not need further modification. - On-board machine electrical panels contain power equipment, control, signalling and monitoring devices. This panel is used by the machine operator to operate and control the machine and is usually fitted downstream of the electrical power delivery point that powers the machinery.
The on-board industrial electrical panel contains all types of power and control equipment: meters, automatic circuit breakers, shunting switches, drives, measuring devices, relays: all critical components for the correct and effective operation of the automated machine.
On the side or external surfaces, the various control components are positioned between pushbuttons and selector switches, or even lamps and indicator LEDs for good signalling. These are all instruments used by the operators themselves for the use of the industrial machine.
It is essential to consult professional and experienced technicians: one single mistake in the design and implementation of the electrical panel could cause damage to the site, the machine itself and to people. It is precisely for this reason that the standards of functionality and safety must be very high, not only for the installation of the electrical panel and its correct configuration but also for the periodic maintenance to always ensure its excellent reliability and continuity in the company production.
A key part of the entire process is considering all the environmental factors that, within certain limits, could alter the functionality of the machine itself. Thus, conditions of humidity, altitude, vibration and various stresses, electromagnetic compatibility and temperature will be taken into account during the design phase, to avert all kinds of risks and malfunctions, according to the standards currently in force. - • Finally, we have the electrical panels for the diagnostics of simple or complex equipment, or even just parts of wiring or machines. This panel is particularly popular in the automotive, agricultural machinery, medical, earth moving machinery and oil-hydraulics sectors: the scope of application is quite vast, covering all types of equipment for professional use.
Looking for more information about our services?
Discover what we can do for your company.
Next Event: MECSPE
We are excited to participate in MECSPE 2025, the leading trade fair for the subcontracting industry.
Visit us at Hall 28 – Stand B01 from March 5th to 7th, 2025!
Discover how Cablotech is driving innovation in electrical wiring, panels and electromechanical assembly.